Before the SCBA workshop was modernised, Hertwig and his coworkers cleaned everything manually, except the BA masks, which were washed in a household dishwasher. ‘We could fit 18 in the dishwasher, which ran for two hours,’ he recalls. But that's a thing of the past now. The around 2,000 BA masks per year are now cleaned much more quickly and reliably – thanks to MEIKO technology and the ambitious planning of Jens Jacobsen, head of sales for personal protective equipment at MEIKO. Since the modernisation, everything can be done during regular working hours of full-time staff.
Three cycles were considered during planning: the SCBA workshop, the hose workshop and the laundry. MEIKO placed a focus on SCBA technician safety. Word has gotten out about the model workshop, and SCBA technicians from all over Germany journey to Offenburg for inspiration.
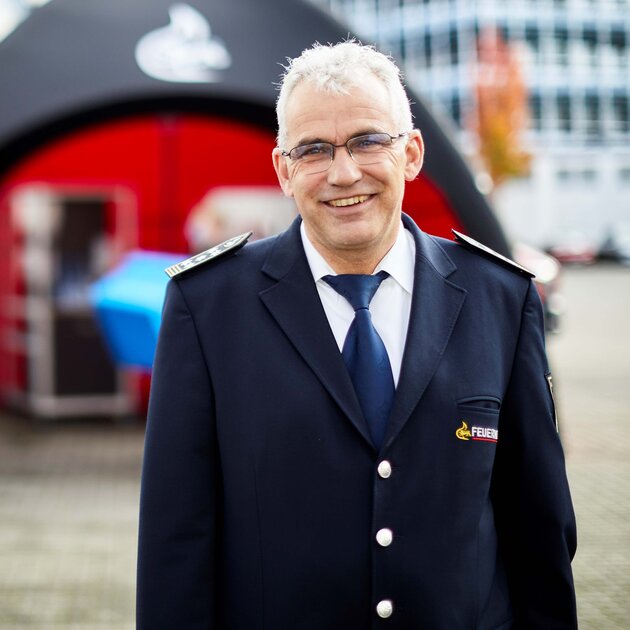
With MEIKO we have established a truly great process in the SCBA workshop.
Peter Schwinn, commander at Offenburg fire service
Systematic planning: separation of dirty and clean areas, ergonomics and efficiency
Packed in a transport crate, the used equipment is placed on a drain table in the SCBA workshop. During unpacking, any toxic substances are removed by an extraction system built in the floor. At the same time, an air curtain protects the SCBA technician from above. Fresh air flows down from the ceiling and separates contaminated equipment behind the curtain from the SCBA technician ‘operating’ in front of it – similar to the conditions for a surgeon in an operating room.
Pre-cleaning
MEIKO's concept included strict separation of clean and dirty sides, ergonomics and maximum efficiency. This is why the drain table is followed by a TopClean D from MEIKO for pre-cleaning of the respiratory protective equipment. The appliance enables decontamination of harmful substances such as soot, which is hydrophobic and therefore cannot be simply rinsed off under running water. TopClean D works with a high water pressure, removing coarse dirt from everything from the BA masks and SCBA harnesses, to cylinders, to the pneumatics. The appliance manages four self-contained breathing apparatuses and 12 BA masks at once. BA masks are stretched out onto heads for BA masks and cleaned from the outside.
The ergonomics are also outstanding: The appliance is located in a corner so that the SCBA technician only has to turn 90 degrees when removing the rack from the TopClean D. This prevents heavy lifting moving forwards and backwards.
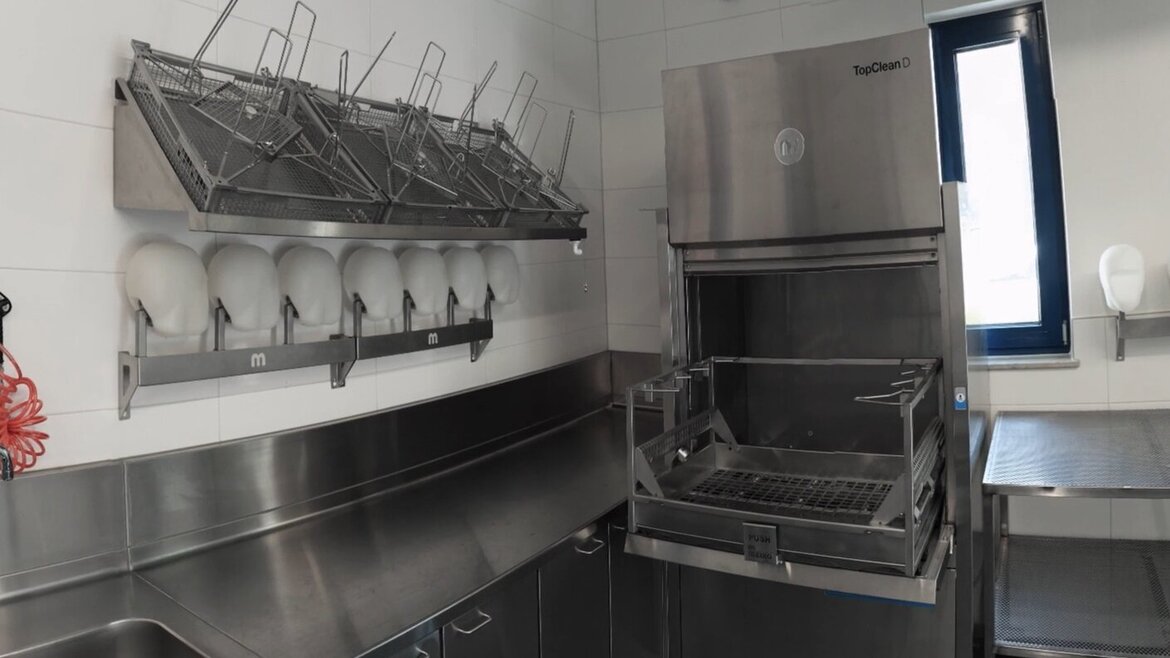
Cleaning and disinfection
The next station: a sufficiently large stainless steel work surface for dismantling the self contained breathing apparatuses. Due to the large volume of objects to be cleaned, the work surface is joined by a TopClean H: a washer-disinfector with an automatic hood system. Specially designed racks are loaded with the BA masks and regulators. Racks with regulators are then ‘connected’ to the machine via quick connect and inserted into the TopClean H. The machine hood automatically lowers and everything, including the inside and outside of the BA masks, is cleaned and disinfected in just minutes. As pre-cleaning already took place in the TopClean D, it is now possible to run the shortest program (about 6 minutes). This saves time and energy.
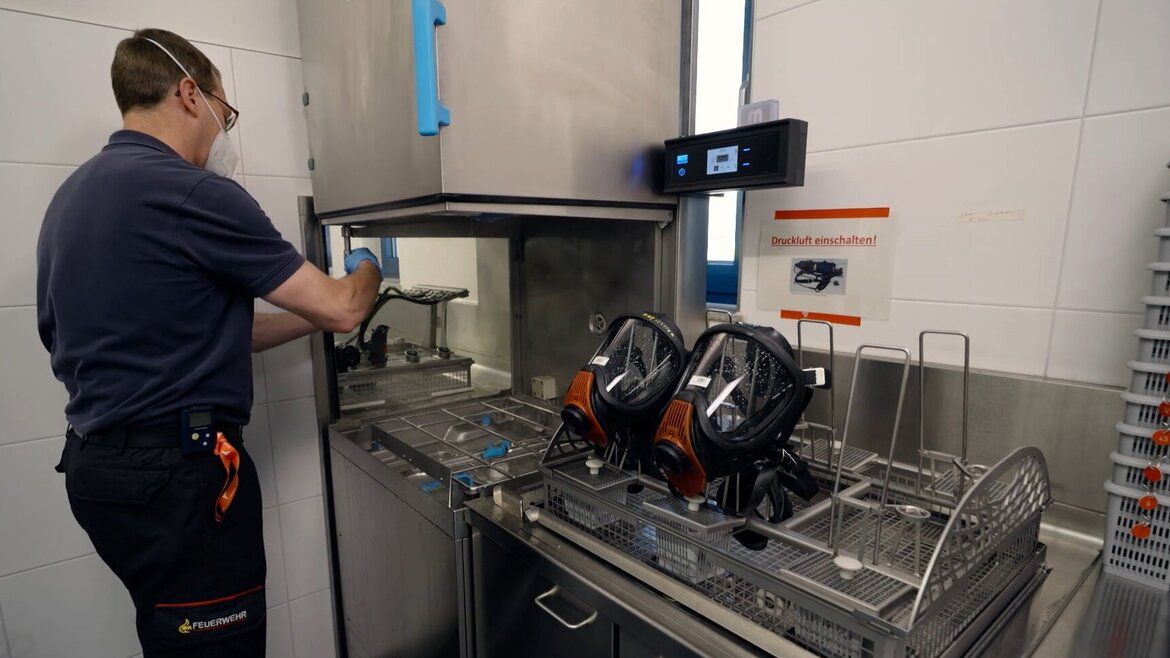
This is followed by a buffer zone in the clean area, which is separated by a wall. An opening in the wall ensures easy transport of the cleaned equipment for drying, reassembly, documentation, packaging and storage. The opening in the wall means the dirty and clean areas are no longer completely separated, but the team in the clean area works under a higher air pressure than in the dirty area. Climate control technology that reduces airborne particles makes it possible. This largely prevents hazardous particles from being transferred through the air. In the clean area, the ‘buffer zone’ is followed by a drying cabinet. This cabinet was placed here by MEIKO in consultation with leading hygiene specialists to prioritize employee health above all else.
Two-stage process developed together
The former commander at Offenburg fire service, Peter Schwinn, appreciated the partnership with MEIKO. Together, they established a truly great process in the SCBA workshop. The process is the result of a very open collaboration and MEIKO's willingness to always consider suggestions made right away.
The most innovative part of the process is the separating of BA mask cleaning into two steps:
- Pre-cleaning from the outside in the TopClean D and
- Disinfection from the outside and inside in the TopClean H – all while saving time and ensuring maximum hygiene safety.
Previously, there was a risk that harmful particles, such as tiny asbestos fibres, could enter the inside of the mask from the outside during pre-cleaning in the soak tank. These particles would not be removed during disinfection, which is meant to eliminate bacteria and viruses. During the next call-out, they were then breathed in by the BA mask wearer. This can no longer happen today, as the particles are removed mechanically in the TopClean D.
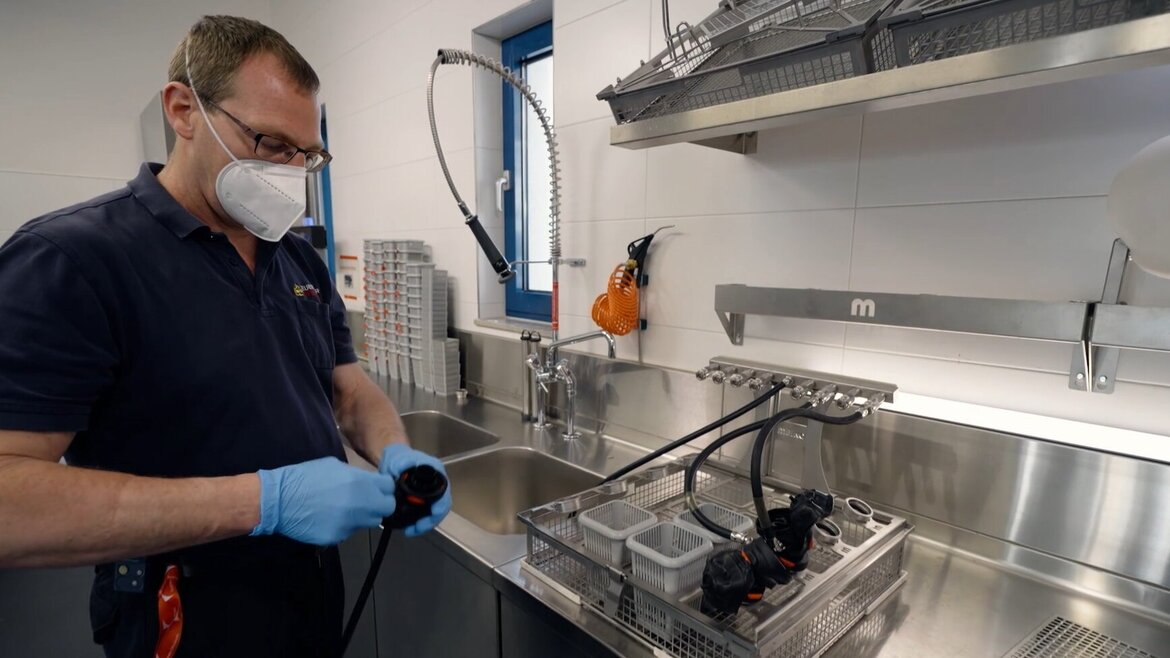
SCBA technician completely satisfied
Martin Hertwig, head of the SCBA workshop, considers the occupational health and safety, the ergonomics and the speed during handling to be crucial advantages: ‘When we were still cleaning things manually, the fire services in our pool were basically out of commission while their equipment was in our shop,’ he recalls. But the fact that he and his coworkers now breathe in as little toxic substances as possible is an invaluable benefit in daily operations.
By planning and outfitting the Offenburg SCBA workshop, MEIKO employees completed a project close to their hearts, proving that they are capable of addressing the individual needs of their customers to realise an optimal solution together. ‘With our machines, we finish the work in just a fraction of the time previously needed, all without additional chemicals and without the materials suffering,’ says Jens Jacobsen, satisfied. What he's especially proud of: ‘We're talking about the maximum possible removal of hazardous substances. It doesn't get any better!’