FROM LUDWIGSHAFEN TO COLOGNE, FROM KARLSRUHE TO ROTTERDAM:
Industrial and petrochemical companies rely on Total Safety as their service provider for everything to do with employee safety. Clean rooms in different facilities are different – is it an oil platform or a refinery? Wherever PPE and respiratory protective equipment are required, absolute safety is a must.
‘We provide our customers with full-package concepts for respiratory protection. We do more than provide masks – we also clean them,’
explains Guido Koch. He is Equipment and Services Manager for Germany and Austria, working from Dorsten in North Rhine-Westphalia, where his role in the American company is to manage the provision of equipment to industrial customers, among other jobs. He coordinates a wide variety of BA masks made by all of the usual manufacturers: they have thousands of overpressure or filter masks in circulation. When they have been used, they return to Total Safety's respiratory protective equipment workshop in Dorsten or Leuna to be hygienically cleaned so they can get through the next tough and, crucially, mucky assignment.
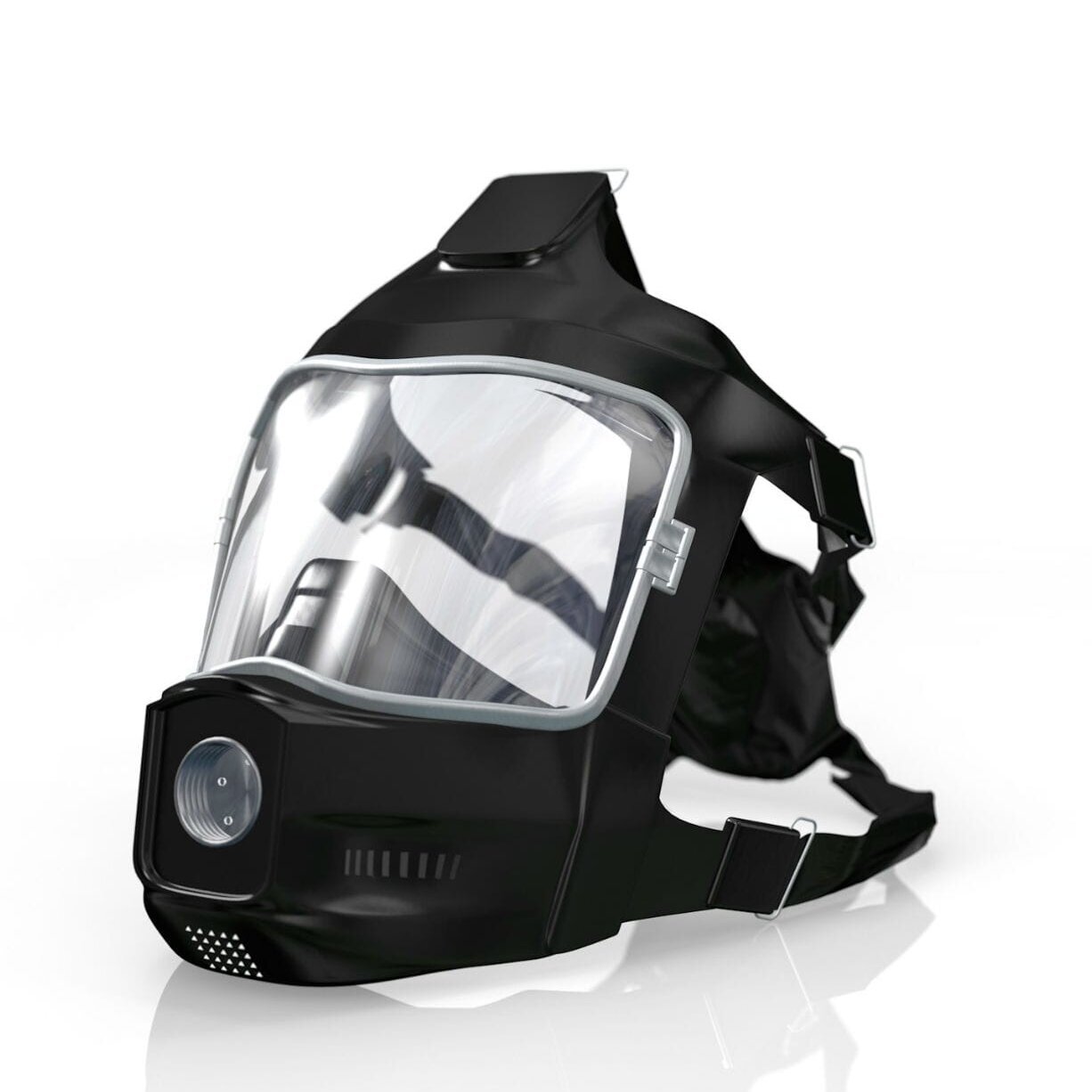
One such project on a grand scale was an audit at an oil company. Operations stopped for two months while everything was cleaned, inspected and maintained.
‘In the peak periods, we had up to 4,500 items of respiratory protective equipment coming through the workshop in seven days. That is a task that cannot be met by hand,’
says Guido Koch. Thankfully, his mechanical colleague, the MEIKO TopClean M, contributes the lion's share of the work 24/7.
‘We have volunteer firefighters on our team who could not get their heads around how it would be possible to clean this volume of respiratory protective equipment in such a short period of time,’
remembers Guido Koch. The team in Dorsten managed it, though – and Total Safety delivered total safety.
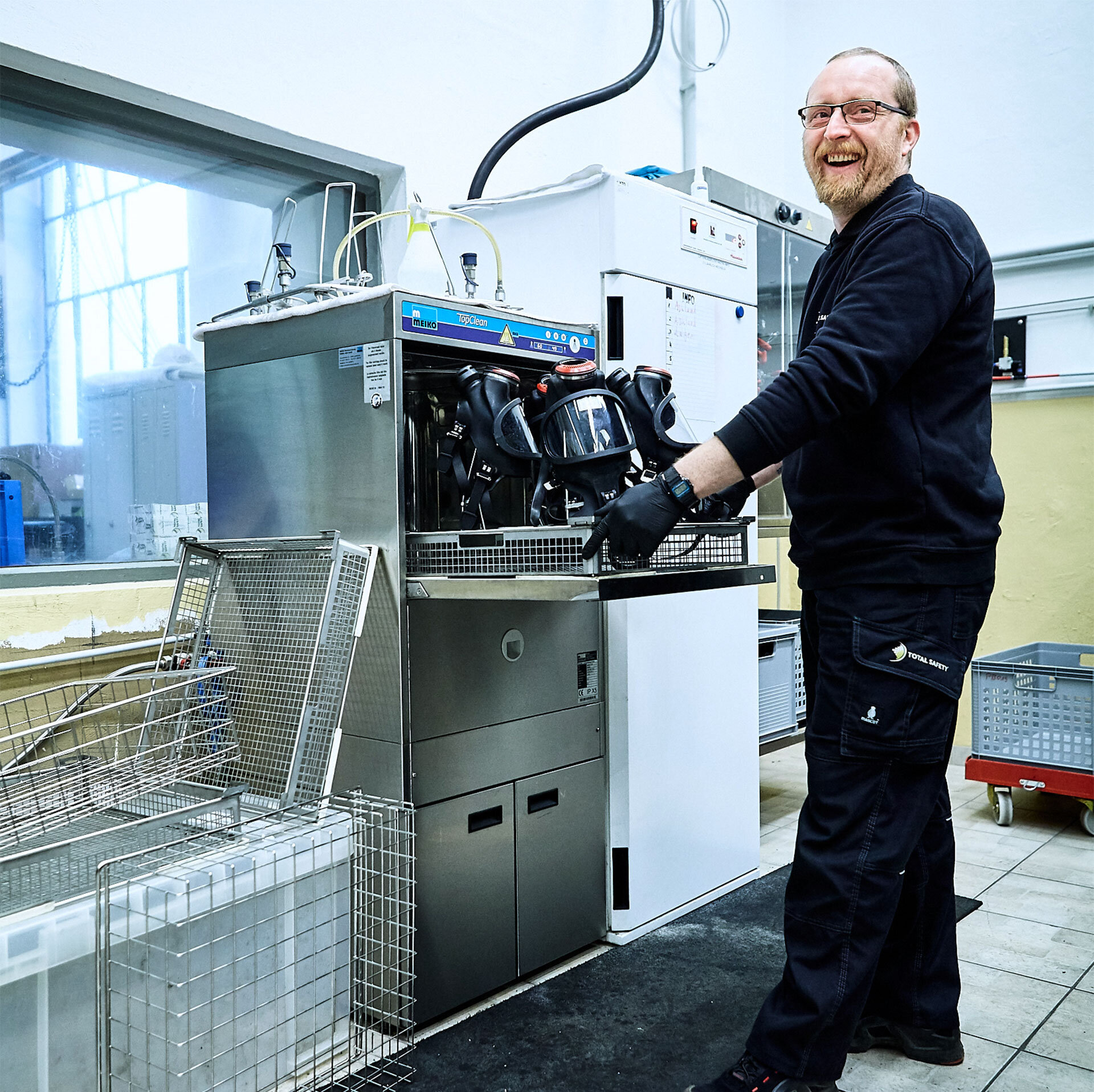
Having the mask cleaning machine in continuous operation impressed the team in the respiratory protective equipment workshop, even though they were already fans of the TopClean M. Even Guido Koch says,
‘This intensive week was incredibly impressive but just thinking about general use: the machine has been running eight to ten hours a day, five days a week for almost two years with no breakdowns. That is already remarkable! And our employees can work well, quickly and, most importantly, safely.’